In today's rapidly evolving technological landscape, the term "Desifake" has emerged as a significant concept tied to the rise of digital fabrication in modern industries. As companies embrace advanced manufacturing techniques, understanding Desifake becomes crucial for staying competitive. This phenomenon represents the intersection of digital innovation and traditional manufacturing, paving the way for transformative changes across various sectors. By exploring its implications, businesses can unlock new opportunities for growth and efficiency.
Digital fabrication, often associated with Desifake, refers to the process of creating physical objects from digital designs using advanced technologies such as 3D printing, CNC machining, and laser cutting. These innovations have revolutionized how products are conceptualized, designed, and produced. Industries ranging from automotive to healthcare are leveraging these tools to streamline production, reduce costs, and enhance product quality.
As we delve deeper into this topic, it is essential to recognize the impact of Desifake on global supply chains and manufacturing processes. This article will provide a comprehensive overview of Desifake, its applications, challenges, and future prospects. By the end, you will have a clearer understanding of how digital fabrication is reshaping the modern industrial landscape.
Read also:Scarlett Johansson Swim Exploring The Iconic Moments And Stories
Table of Contents
- What is Desifake?
- History of Digital Fabrication
- Key Technologies in Digital Fabrication
- Applications of Desifake in Modern Industries
- Benefits of Digital Fabrication
- Challenges Facing Digital Fabrication
- Future Trends in Desifake
- Case Studies: Successful Implementation of Desifake
- Ethical Considerations in Digital Fabrication
- Conclusion and Call to Action
What is Desifake?
Desifake is a term that encapsulates the integration of digital technologies into the fabrication process, enabling the creation of complex designs with precision and efficiency. It involves the use of software and hardware to transform digital blueprints into tangible products. This approach has gained traction due to its ability to reduce waste, lower production costs, and increase customization options.
At its core, Desifake represents the convergence of design and manufacturing. By leveraging technologies such as CAD (Computer-Aided Design) and CAM (Computer-Aided Manufacturing), businesses can create prototypes and final products with remarkable accuracy. This shift from traditional manufacturing methods to digital fabrication marks a pivotal moment in industrial evolution.
Defining Digital Fabrication
Digital fabrication refers to the process of using computer-controlled machines to create physical objects from digital models. This method allows for greater flexibility and adaptability in production, making it ideal for industries that require rapid prototyping and customization. Some key characteristics of digital fabrication include:
- High precision in manufacturing
- Reduced material waste
- Increased speed in production
- Enhanced ability to customize products
History of Digital Fabrication
The origins of digital fabrication can be traced back to the mid-20th century when early computer-controlled machines were first developed. Over the decades, advancements in technology have led to the creation of more sophisticated tools and processes. Today, digital fabrication is a cornerstone of modern manufacturing, driving innovation across various industries.
Key Milestones in Digital Fabrication
Several milestones have marked the evolution of digital fabrication:
- 1950s: Development of the first numerically controlled (NC) machines
- 1980s: Introduction of 3D printing technology
- 2000s: Widespread adoption of CAD and CAM software
- 2010s: Emergence of additive manufacturing as a mainstream production method
Key Technologies in Digital Fabrication
Several technologies underpin the success of digital fabrication, each contributing to its versatility and effectiveness. These include:
Read also:Exploring The Captivating World Of O2tv Series A Deep Dive Into Entertainment
3D Printing
3D printing, also known as additive manufacturing, involves building objects layer by layer based on a digital model. This technology has revolutionized product development by enabling rapid prototyping and reducing the need for tooling. Industries such as aerospace, automotive, and healthcare have embraced 3D printing to create complex components with high precision.
CNC Machining
Computer Numerical Control (CNC) machining is a subtractive manufacturing process that uses computer-controlled tools to remove material from a workpiece. This method is ideal for producing parts with intricate geometries and tight tolerances. CNC machining is widely used in industries requiring high-precision components, such as electronics and medical devices.
Applications of Desifake in Modern Industries
Desifake has found applications in a wide range of industries, each benefiting from the unique advantages it offers. Below are some notable examples:
Automotive Industry
In the automotive sector, digital fabrication is used to create prototypes, tooling, and production parts. Manufacturers leverage 3D printing to produce lightweight components, reducing vehicle weight and improving fuel efficiency. Additionally, CNC machining ensures the production of high-quality parts with minimal waste.
Healthcare Sector
The healthcare industry has embraced digital fabrication for creating custom medical devices, prosthetics, and implants. 3D printing allows for the production of patient-specific solutions, enhancing treatment outcomes. For instance, surgeons can use 3D-printed models to plan complex procedures, improving accuracy and reducing risks.
Benefits of Digital Fabrication
The adoption of digital fabrication offers numerous advantages, making it an attractive option for businesses seeking to innovate and optimize their operations. Some key benefits include:
- Increased efficiency in production processes
- Enhanced ability to customize products for individual customers
- Reduced lead times for product development and manufacturing
- Lower costs associated with tooling and material waste
Challenges Facing Digital Fabrication
Despite its many advantages, digital fabrication faces several challenges that must be addressed to ensure its continued growth and success. These challenges include:
High Initial Costs
Investing in digital fabrication technologies can be costly, particularly for small and medium-sized enterprises. The expense of purchasing equipment and training personnel may pose a barrier to entry for some businesses.
Material Limitations
While digital fabrication offers a wide range of materials, there are still limitations in terms of strength, durability, and cost. Researchers continue to explore new materials that can meet the demands of various industries while remaining affordable.
Future Trends in Desifake
As technology continues to advance, the future of Desifake looks promising. Emerging trends such as artificial intelligence, machine learning, and the Internet of Things (IoT) are expected to further enhance digital fabrication capabilities. These innovations will enable smarter, more connected manufacturing processes that can adapt to changing demands in real time.
Predictive Maintenance
By integrating IoT sensors into digital fabrication systems, manufacturers can monitor equipment performance and predict maintenance needs. This proactive approach reduces downtime and extends the lifespan of machinery, improving overall efficiency.
Case Studies: Successful Implementation of Desifake
Several companies have successfully implemented Desifake, achieving remarkable results. Below are two notable examples:
Case Study 1: General Electric
General Electric (GE) has embraced additive manufacturing to produce complex components for its aviation division. By using 3D printing, GE has reduced production times and costs while improving the performance of its jet engines. This success demonstrates the potential of Desifake in transforming traditional manufacturing processes.
Case Study 2: Adidas
Adidas has leveraged digital fabrication to create customized footwear for its customers. Using 3D printing technology, the company can produce unique designs tailored to individual preferences. This approach not only enhances customer satisfaction but also differentiates Adidas from its competitors.
Ethical Considerations in Digital Fabrication
As with any technological advancement, digital fabrication raises ethical concerns that must be addressed. Issues such as intellectual property rights, environmental impact, and job displacement require careful consideration to ensure responsible adoption of these technologies.
Intellectual Property Rights
With the ease of replicating digital designs, protecting intellectual property becomes a significant challenge. Manufacturers must implement robust security measures to safeguard their proprietary designs from unauthorized use.
Conclusion and Call to Action
In conclusion, understanding Desifake and its role in the rise of digital fabrication is essential for businesses seeking to thrive in today's competitive landscape. By embracing these technologies, companies can unlock new opportunities for growth, efficiency, and innovation. However, it is crucial to address the challenges and ethical considerations associated with digital fabrication to ensure its responsible and sustainable development.
We invite you to share your thoughts and experiences with Desifake in the comments section below. Additionally, explore our other articles to learn more about the latest trends and innovations in the world of digital fabrication. Together, let's shape the future of modern industries through collaboration and knowledge-sharing.
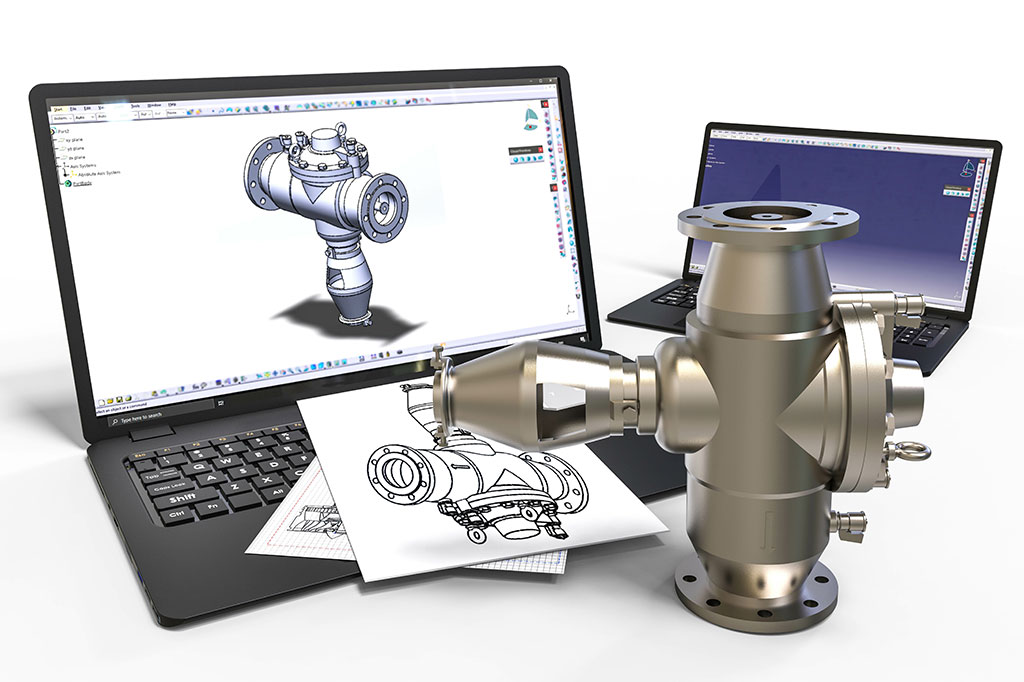
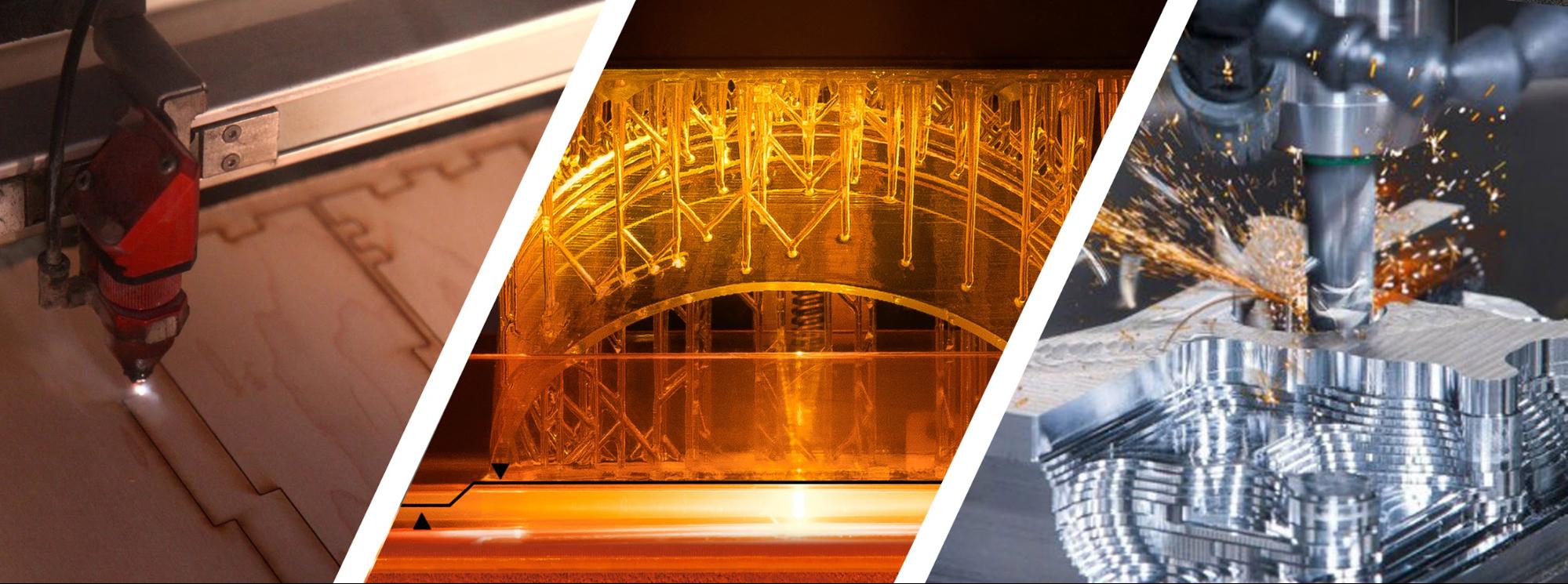
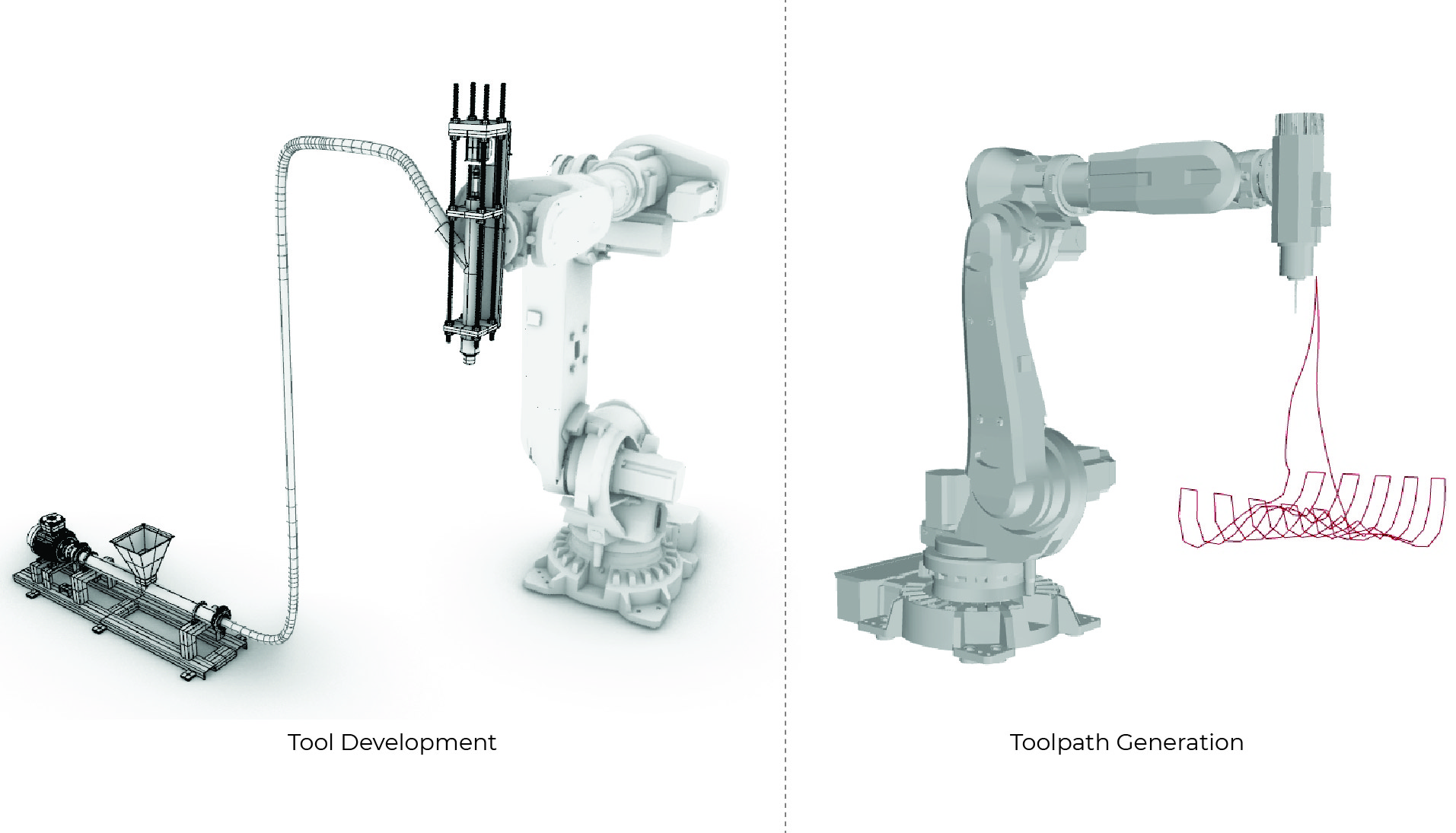